
In development of HD3D, Siemens PLM has combined its experience in data manipulation and management (with Teamcenter), lightweight viewing (with the JT format) and large scale visualisation and built a technology. For example, this could be a peep at where development efforts are being concentrated (by filtering and visualising parts or sub-assemblies under work – in itself derived from change status), what parts are being outsourced, or where costs or weight are found (by filtering for parts within specific cost or mass ranges). This can then be explored and visualised, and details delved into when needed and filtered to access the exact information required. HD3D provides a framework that’s delivered in both NX and Teamcenter and allows users to take the graphically rich 3D data and gain access to the metadata underneath it. Note that non-critical geometry is made transparent, providing a clear view, but maintaining context
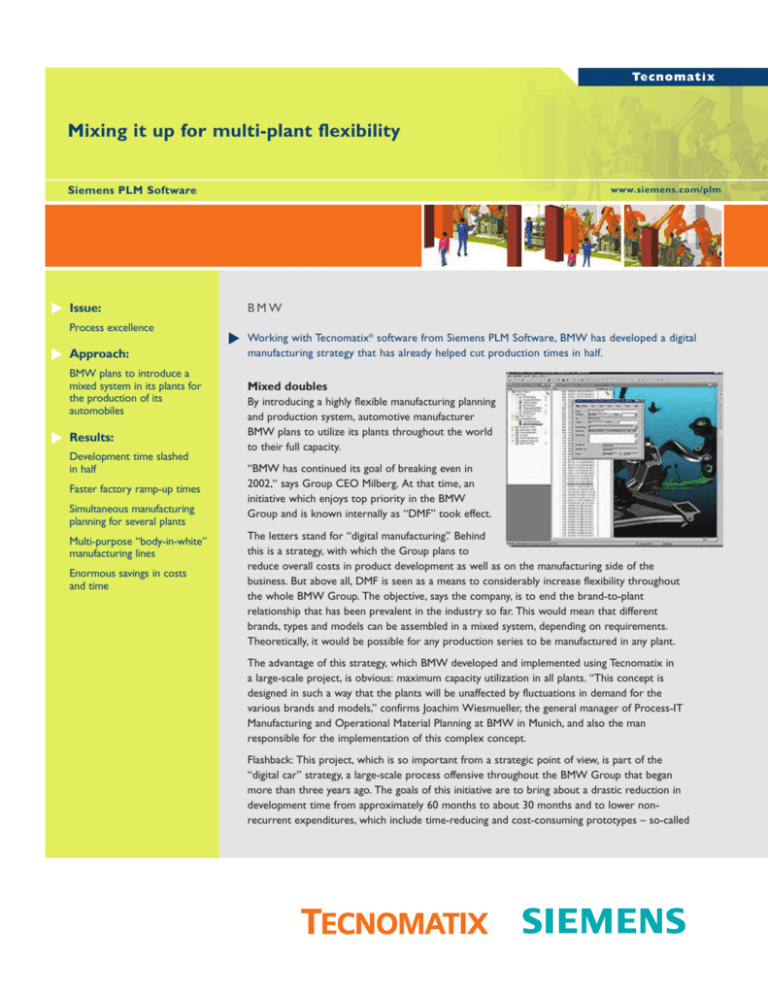
Components are grouped and tagged by sub-system categorisation allowing users to see the stage each department has reached. The problem is, despite all of their best intentions, the two products don’t exactly work together.Ī complex assembly of a Fiat 500 is loaded and the data stripped back to reveal the power and drive train details. In the case of Siemens PLM, for geometry that’s NX (or a 3D viewing technology) and for metadata Teamcenter. To find both, you typically need to use two different systems. However, the problem is, unless you have a very intimate knowledge of where that data is stored, who created it and what you’re actually looking for, it’s very hard to get an idea of where a product is at.ģD datasets contain the form, and metadata is attached to each part, sub-assembly and sub-system in the shape of documents (text, spreadsheets, PDFs, CAD data etc). In short, that’s a substantial amount of data. Those two technologies have the ability to fully document a product, not only in terms of it’s form and function, but also in terms of the information that relates to its development, manufacture, lifecycle and eventual retirement. Take the average design and engineering organisation for example, that’s fully adopted both 3D design and PLM.
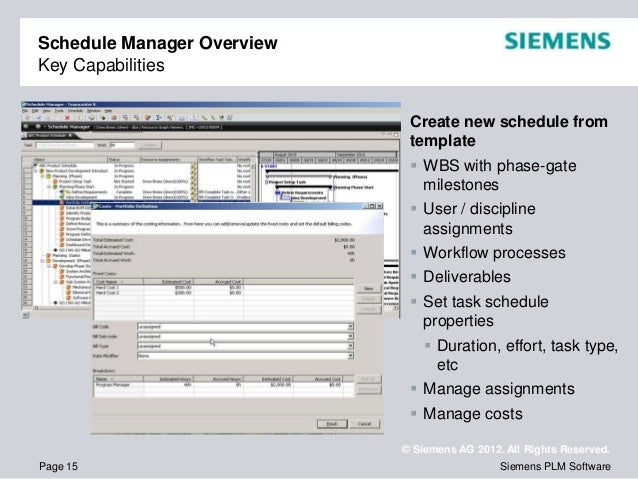
Parts and sub-systems are colour coded and categorised by supplier, enabling users to see exactly where the products are sourced from A visual report is run on the same assembly, but using supplier metadata as the source for the search.
